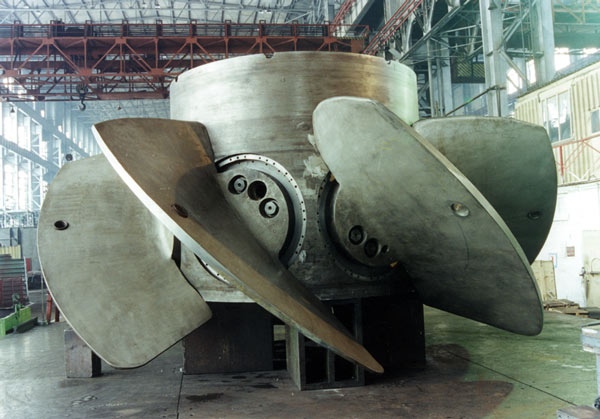
Высокое качество изготовления турбин при одновременном сокращении трудоемкости и цикла их производства является результатом внедрения новых решений по всему технологическому циклу.
Наиболее существенные и прогрессивные новшества, связанные с глубокой подготовкой производства, потребовали переоснащения и замены устаревшего оборудования, проведенных на основе технико-экономического анализа, выполненного при разработке проекта турбины; 92% общей массы турбины составляют сварные конструкции.
В их числе рабочее колесо, статор, спиральная камера, все кольцевые детали направляющего аппарата и др. Обеспечение производства их на современном уровне требований стало возможным в результате перевооружения раскройно-заготовительного цеха. Здесь созданы и функционируют три комплексно-механизированные линии изготовления заготовок из листового проката.
Основа этих линий — газо-резательные машины с числовым программным управлением, обеспечивающие высокую точность вырезки и комплексное повышение производительности труда. Одновременно с вырезкой по контуру выполняются фаски под сварку. Машина обслуживается одним оператором-газорезчиком.
Впервые в отрасли разработка программ для этих машин осуществляется в специально созданном программирующем центре с применением электронно-вычислительной техники и средств программного обеспечения. Внедрение новой системы обеспечило также повышение коэффициента использования листового проката. Высокоточное изготовление листовых заготовок разверток звеньев спиральной камеры в сочетании с новой системой проверки звеньев после гибки позволило отказаться от весьма трудоемкой и требующей большой производственной площади общей контрольной сборки узла на заводе. Сборка первых двух спиральных камер на ГЭС показала хорошую их собираемость.
Рабочее колесо является определяющим узлом в производстве гидротурбин. Для Саяно-Шушенской ГЭС необходимо изготовить два типа колеса: сменное и штатное. Сменные рабочие колеса изготовлены из низколегированной стали. Защита лопастей этих колес от действия кавитации осуществлена облицеванием лопастей тонколистовой нержавеющей сталью с .применением высокопроизводительной и обеспечивающей стабильное качество сварки взрывом. Эта работа выполнялась совместно с институтом АНИТИМ. При подготовке и освоении новой технологии были решены сложные технологические (
параметры опоры, процесс сварки и последующая термообработка лопастей) и организационные вопросы. Работа выполнялась в полевых условиях.
Штатные рабочие колеса выполняются сварными из нержавеющей стали 00×12НЗД диаметром 6,77 м, лопасти — из листового проката методом штампо-гибки. Крупной проблемой является изготовление верхнего обода штатного РК из нержавеющей стали. Верхний обод имеет диаметр 6,5 м и массу 72 т. Изготовление цельнолитого верхнего обода в настоящее время представляет собой трудную металлургическую и транспортную задачу. Принято решение изготовить верхний обод из двух частей. Трудность заключается еще и в том, что верхний обод имеет сложную конфигурацию и большую переменность толщин 150—400 мм.
Для обеспечения высокого качества сварных узлов особое внимание уделено широкому применению неразрушающих методов контроля.
Металлургическим производством также решены вопросы изготовления лопаток направляющего аппарата из нержавеющей стали марки 0×12НДЛ. Применение ПО «Ижорский завод» вертикальной формовки и заливки значительно улучшило качество поверхности и точность отливок.
Наиболее прогрессивные методы (
точное литье по выплавляемым моделям и штамповка) применены на ЛМЗ для изготовления ряда деталей индивидуальных сервомоторов и системы управления ими. Впервые в нашей практике вместо совместной расточки отверстий под припасованные болты в соединении вала турбины со сменными рабочими колесами применена обработка их в каждой детали отдельно по специальному кондуктору. После соответствующей отработки эта технология может стать основной на данном объединении.
Новый способ обработки отверстий под подшипники цапф лопаток в крышке турбины и нижнем кольце направляющего аппарата с использованием технологических колец позволил отказаться от громоздкой операции контрольной сборки узла в цехе. Проверка соосности отверстий осуществляется специальными калибрами на максимально сближенных деталях. Новая технология не только сократила трудоемкость сборочных работ и цикл производства, но и повысила точность взаимного расположения подшипников цапф лопаток.
Технологами объединения разработана и внедрена
комплексная технология с применением большого количества прогрессивного и оригинального специального оснащения для обработки индивидуальных сервомоторов направляющего аппарата и системы управления ими. Сборка и испытание головного образца направляющего аппарата подтвердили возможность получения необходимой стабильности размеров при обработке отдельных деталей. Весь комплекс технологической подготовки производства обеспечил своевременное и высококачественное изготовление уникальных гидротурбин. Заготовки всех основных деталей: рабочих колес, вала, лопаток направляющего аппарата, колонны статора поставляет ПО «Ижорский завод».
Выводы.1. Созданная гидротурбина мощностью 650 МВт, способная развивать максимальную мощность 735 МВт, с КПД около 96% соответствует лучшим мировым образцам и является новым шагом в развитии отечественного энергомашиностроения.
2. Применение новых методов научно-исследовательских работ, конструкторско-технологических решений, освоение новых способов изготовления позволили сократить создание гидротурбинного оборудования на один год.
3. Досрочное изготовление гидротурбинного оборудования, а также применение сменных рабочих колес и других конструкторских и монтажных решений позволили на два года раньше срока пустить первый агрегат еще при недостроенной плотине.